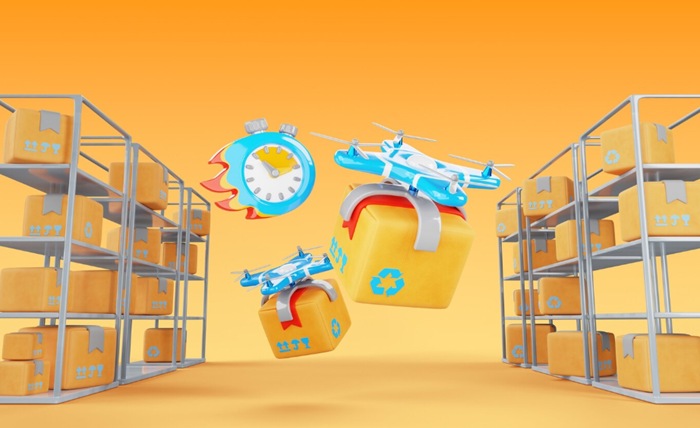
Order fulfillment has come a long way from the days of paper pick lists and manual inventory checks. As customer expectations continue to rise, businesses are under increasing pressure to deliver orders faster, with greater accuracy, and at lower costs. From small retailers to large-scale logistics providers, the entire fulfillment process has been reshaped by new technology, automation, and smarter strategies. What once took days or even weeks can now be achieved in mere hours. This evolution isn’t just about speed—it’s about transforming how companies manage inventory, process orders, and ensure customer satisfaction.
From Manual to Automated: The First Leap
In the early stages of retail and logistics, fulfillment was largely manual. Warehouse staff would receive printed orders, locate items by memory or basic labeling systems, and pack them for shipment. Errors were frequent, and scaling operations was difficult. The introduction of barcode scanners and basic warehouse management systems (WMS) in the 1980s marked a turning point, allowing businesses to track inventory more accurately and reduce human error.
The 1990s and early 2000s brought another shift with the rise of e-commerce. Retailers had to adapt to individual orders instead of bulk shipments, prompting a wave of innovation in fulfillment technology. Software platforms evolved to support real-time inventory updates, better tracking, and tighter integration with sales channels. This laid the groundwork for the high-speed, high-volume fulfillment we see today.
Smarter Warehousing with Technology
Modern warehouses no longer rely solely on human labor and paper-based processes. Today’s fulfillment centers are equipped with smart technologies that improve efficiency across the board. Robotics and automated guided vehicles (AGVs) are now common in large facilities, navigating aisles and transporting items to packing stations without human intervention.
Artificial intelligence (AI) and machine learning are also playing critical roles. AI-driven systems can forecast demand, optimize picking routes, and allocate resources dynamically. These smart tools don’t just reduce labor costs—they make the fulfillment process more adaptable and precise.
One key innovation is real-time data visibility. Cloud-based WMS platforms allow businesses to monitor order status, stock levels, and shipment progress from anywhere. This level of insight improves decision-making and ensures that fulfillment operations can pivot quickly in response to changes in demand or supply chain disruptions.
The Role of Last-Mile Logistics
While automation within the warehouse has improved, the “last mile” of delivery—getting the product from the fulfillment center to the customer—is still one of the most complex parts of the process. With the growth of same-day and next-day delivery expectations, companies have had to rethink how they approach this final leg.
Crowdsourced delivery models, local micro-fulfillment centers, and partnerships with third-party logistics (3PL) providers are some of the ways businesses have responded. These strategies allow companies to move inventory closer to customers and shorten delivery times significantly.
In addition, the rise of route optimization software helps delivery drivers complete more orders in less time, while reducing fuel costs and environmental impact. The integration of GPS tracking and customer-facing delivery updates further enhances the overall experience.
Fulfillment as a Competitive Edge
Fast, accurate fulfillment is no longer a back-end operation—it’s a key part of the customer experience. Delays, stockouts, or errors can quickly erode customer trust and loyalty. On the other hand, efficient fulfillment can differentiate a brand and foster repeat business.
This shift has led many businesses to rethink their fulfillment strategies entirely. Some invest in their own advanced fulfillment centers, while others partner with experienced logistics providers to scale quickly and meet demand. For instance, working with a fulfilment company UK based businesses trust can provide the flexibility and speed needed to stay competitive without massive upfront investment.
Sustainability and the Future of Fulfillment
As fulfillment continues to evolve, sustainability is becoming a central concern. Customers and regulators alike are pushing for greener operations. This includes reducing packaging waste, optimizing shipping routes to lower emissions, and adopting energy-efficient technologies within fulfillment centers.
Looking ahead, the future of order fulfillment will likely involve even more automation, personalization, and sustainability. Drones and autonomous vehicles may eventually handle local deliveries. AI will become even more predictive, allowing for hyper-efficient inventory planning. Fulfillment centers will continue to shrink in size and move closer to urban centers, ensuring faster service without sacrificing environmental responsibility.
Conclusion
The evolution of order fulfillment has transformed how businesses operate and how customers shop. It’s faster, smarter, and more customer-centric than ever before. From AI-powered warehouses to innovative last-mile solutions, companies that embrace modern fulfillment practices are positioning themselves for success in an increasingly competitive market. As technology continues to evolve, so too will the standards for what constitutes “great” fulfillment—making it not just a logistical necessity, but a strategic advantage.